Thermoplastics are a versatile group of plastics that can be repeatedly melted and reformed. This property makes them highly suitable materials for injection molding, which is a popular manufacturing process to mass produce plastic parts.
Injection molding involves heating thermoplastic materials to a molten state, injecting them into a mold, letting them cool and solidify into the desired shape before ejecting the finished part. The fact that thermoplastics can transition between molten and solid states is key to their suitability for injection molding.
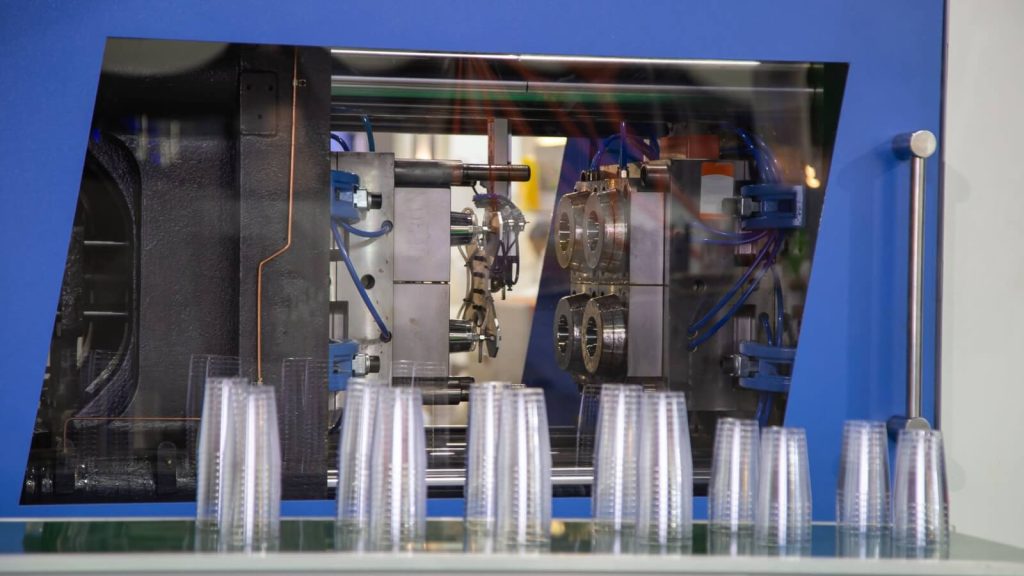
Can thermoplastics be injection molded?
Yes, thermoplastics are the most commonly used materials for injection molding. Their unique physical properties allow them to be injection molded repeatedly, making them ideal for mass production.
In this article, as a professional plastic injection molding manufacturer, we’ll explore why thermoplastics work so well with injection molding and the reasons behind their widespread use. We’ll also look at the most popular thermoplastics used with this technique. Buckle up for an in-depth guide on successfully injection molding thermoplastic materials!
Why Are Thermoplastics Ideal for Injection Molding?
Thermoplastics owe their popularity in injection molding to several useful characteristics:
1. Repeatedly Meltable and Solidifiable
The main reason thermoplastics excel in injection molding is their ability to transition repeatedly between molten and solid states.
Can thermoplastics be injection molded? Absolutely! Heating turns them into a liquid which fills mold cavities. Cooling returns them to a solid state retaining the molded shape.
This physical change is 100% reversible and allows using the same thermoplastic material over multiple molding cycles. Thermoplastics can be injection molded, cooled, reheated and remolded without material degradation or change in properties.
2. Rapid Cooling and Solidification
Another useful property is that thermoplastics cool and solidify rapidly compared to metals and alloys. Faster cooling equals shorter production cycles and higher manufacturing throughput.
The fast-cooling property also results in good dimensional stability. Parts cool into solid molded shapes accurately reflecting the mold cavity with minimal post-production shrinkage.
3. Flow Readily in Molten State
In their molten state, thermoplastics flow easily under pressure, filling intricate mold details accurately. Their free-flowing nature allows producing complex, high precision plastic components via injection molding.
Combined with rapid cooling, this gives remarkably accurate end products straight out of the mold. Little or no additional finishing is required with injection molded thermoplastic parts.
4. Wide Choice of Materials
Thermoplastics encompass a broad range of polymers with diverse mechanical and thermal traits tailored to varied applications. Popular materials include polyethylene, polypropylene, ABS, nylon, and PVC.
Polycarbonate and acetal offer high strength-to-weight ratios combined with temperature resistance making them suitable for demanding applications. The wide material selection provides design flexibility not seen with other manufacturing techniques.
Common Thermoplastics for Injection Molding
With hundreds of grades and polymer variants, choosing the right thermoplastic material can get confusing. To simplify selection, here are the most frequently used:
1. Polypropylene (PP)
Polypropylene is a versatile, low-cost polymer used extensively in injection molding consumer products. Offering good chemical resistance with weldable and machinable grades, polypropylene parts have excellent fatigue strength.
Typical applications: Food containers, appliances, automotive parts, industrial components.
2. Acrylonitrile Butadiene Styrene (ABS)
Well known for Lego bricks, ABS combines strength, rigidity and toughness with ease of machining and coating. ABS is also UV-stable allowing colorful injection molded parts.
Typical applications: Toys, auto parts, electronics enclosures, home appliances.
3. Polyamide (Nylon)
Highly versatile engineering thermoplastic, nylon offers impressive mechanical properties. With good wear resistance and chemical stability across temperature extremes, it replaces metals in many applications.
Typical applications: Gears, bearings, fasteners, valves, sporting goods.
4. Polycarbonate
Optically clear high-performance thermoplastic noted for dimensional stability and impact resistance. Used instead of glass for transparency combined with toughness. Withstands higher temperatures than other clear thermoplastics.
Typical applications: Automotive lenses, optics, protective gear, electronics.
5. Polyethylene (PE)
Most mass produced plastic globally, polyethylene comes in various densities suited for different applications. Offers chemical resistance coupled with ductility and low moisture absorption. Recyclable and reusable grades available.
Typical applications: Films, bags, bottles, containers, pipes, household goods.
With technology refinements and new polymer blends constantly expanding capabilities, innovative injection molders push thermoplastics into new frontiers.
Can Thermosets Be Injection Molded?
Can thermoplastics be injection molded? Absolutely! But how about thermosets? These plastics feature heavily cross-linked polymer structures offering exceptional heat resistance combined with dimensional stability across temperature fluctuations.
However, cross-linked thermoset polymers prevent remolding capability, ruling out most conventional injection molding techniques. Instead, specialized injection molding methods have been developed to process thermosetting plastics.
Reaction Injection Molding (RIM) forces a chemically reactive two-component liquid blend into molds where cross-linking occurs. Alternately, cast thermoset preforms are inserted into molds and compression molded into shapes under heat and pressure.
But requirement for specialized equipment and slower cycle times limit thermoset injection molding. Where possible, thermoplastics make a better material choice offering recycling and speed advantages.
Summing Up Thermoplastics Injection Molding
The reversible physical state change between molten liquid and solid plastic is the winning aspect that cements thermoplastics as preferred materials for injection molding applications. Repeated remoldability without material degradation enables mass production of plastic parts via this high precision, reliable manufacturing technique.