Thermoset polymers have some unique properties that make them suitable for certain injection molding applications. However, using them does come with some challenges. In this comprehensive guide, as a professional plastic injection molding manufacturer, I’ll cover everything you need to know about using thermosets in injection molding, including:
- The pros and cons of thermoset injection molding
- How the process differs from thermoplastic injection molding
- What applications are possible with this technology
- Examples of products made from thermoset injection molding
So if you’re wondering whether thermosets can be used in injection molding, read on!
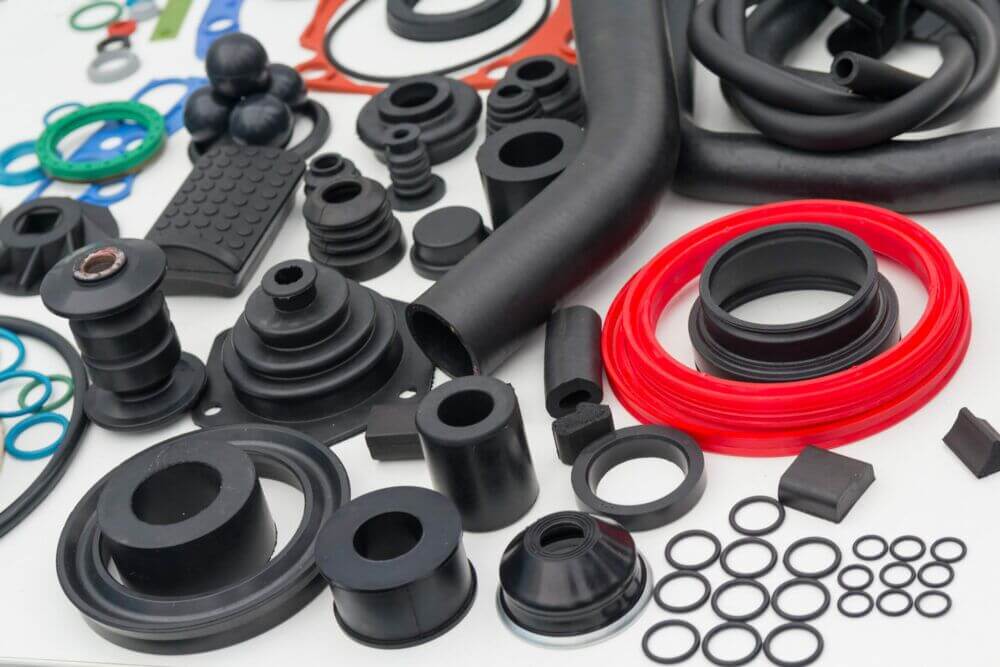
An Overview of Thermoset Polymers
Before we dive into the injection molding applications, let’s quickly cover what thermosets are and what makes them unique.
Thermoset plastics are made up of polymer resins that “set” into a permanent shape after curing. This is in contrast to thermoplastics that soften when heated and can be reshaped.
Some of the key characteristics of thermosets include:
- Heat resistance
- Dimensional stability
- Chemical and corrosion resistance
- High strength
Common thermoset materials used in injection molding include:
- Epoxy
- Unsaturated polyester
- Phenolic resins
- Polyurethanes
- Silicones
Now that you know the basics, let’s look at the pros and cons of using thermosets in injection molding.
The Pros and Cons of Thermoset Injection Molding
The Pros
Here are some of the biggest advantages of injection molding with thermosetting plastics:
Superior heat resistance – Thermosets can withstand temperatures far higher than thermoplastics before deforming. This makes them suitable for high-temperature applications.
Excellent dimensional stability – The cross-linked structure of thermosets means they hold their shape extremely well, even when exposed to heat or solvents. This is useful for precision parts.
Higher strength – Thermosets tend to have higher tensile and compressive strength than thermoplastics. This allows them to perform better under load.
Lower friction – The cross-linked structure results in lower friction characteristics, making thermosets well-suited for bearings and wear parts.
Chemical resistance – Thermosets tend to resist corrosion and degradation from solvents and acids much better than thermoplastics. This is crucial for many industrial applications.
Electrical insulation – The rigid structure of thermosets gives them exceptional dielectric properties to insulate electricity. This is vital for electrical components.
The Cons
However, injection molding with thermosets does come with some downsides:
Higher costs – Both the materials and processing costs tend to be higher compared to thermoplastic injection molding. This can make per-part costs prohibitive for high-volume applications.
Lower impact strength – While strong in tension, thermosets tend to have lower impact resistance and fracture easier unless reinforced. Thermoplastics can have better resilience.
Longer cycle times – The curing reaction required for thermosets means cycle times are longer. This reduces throughput compared to thermoplastics.
Part size limitations – Heating larger parts evenly to cure the thermoset can be difficult, restricting maximum part sizes. Thermoplastics can more easily make very large parts.
Limited color/aesthetic options – Achieving bright colors or clear transparencies with thermosets can require specialized engineering. This restricts styling freedom versus thermoplastics.
Not recyclable – One of the biggest downsides is that cross-linked thermosets cannot be remolded or recycled after curing. Thermoplastics can often be recycled.
So in summary – thermosets excel in heat resistance and dimensional stability but come with processing and cost drawbacks.
How Thermoset Injection Molding Differs from Thermoplastics
The mechanics of injection molding thermosets differs significantly from thermoplastic injection molding:
1. Thermosets are inserted as cold, premixed compounds – Unlike thermoplastics which are melted by heat, thermosets are inserted cold into the injection barrel as a premixed compound containing the base resin and curative additives.
2. Heatappliedinsidethe mold itself – With thermosets, heat is applied inside the injection moldeither through hot water lines or by conducting electricity through the mold walls. This initiates the curing process once the material fills the mold.
3. Much lower injection pressures – Because thermosets flow easily without needing to melt, far lower injection pressures of 500-5000 psi are required compared to 10,000-30,000 psi for thermoplastics.
4. Slower injection speeds – Cycle times for thermoset injection molding average from 2-4 minutes. This compares to less than 1 minute cycles for thermoplastic injection molding.
5. Two-stage injectors – Special two-stage injectors are often needed for thermosets. The first stage meters the cold compound under low pressure before the second stage injects it into the mold.
So in summary, thermoset injection molding relies on applying heat to the mold to cure parts rather than melting plastic inside the injection barrel beforehand. This requires specialized injection machines and processing considerations.
What Applications Are Possible with This Technology?
Thermoset injection molding expands the capabilities of injection molding into applications requiring:
- Continuous temperatures above 250°F
- Constant exposure to fuels, oils, or solvents
- Low moisture absorption
- Minimal part deformation
- Superior electrical insulation
Some of the leading industries using thermoset injection molded components include:
Automotive
Intake manifold gaskets, seals, bushings, ignition components, sensors, and electrical connectors molded from phenolic, silicone, and epoxy.
Aerospace
Lightweight interior panels, brackets, electrical boxes, and ducting molded from BMI composite.
Medical
Precision gears, seals, stopcocks, and catheter parts molded from glass or mineral-filled nylon, acetal, PEEK, ultem, and liquid silicone.
Electronics
Connectors, potting compounds, integrated circuit trays, and switch housings molded from phenolic, silicone, and epoxy.
Industrial
Pump impellers, valve seats, nozzle liners, and bushings molded from phenolic, polyurethane, and acetal.
So while thermoplastics account for over 90% of all injection molded plastics, thermosets occupy vital roles in niche applications.
Examples of Products Made from Thermoset Injection Molding
To give you a better idea of real-world examples, here are some specific products made from thermoset injection molding:
Electrical connectors – Special epoxy formulations allow molding high-temperature connectors able to withstand over 240°C continuously.
Implantable medical parts – Silicone grades certified for medical use can injection mold implants and devices that safely integrate within the human body.
Seals and gaskets – Flexible and rigid thermoset materials mold fluid and air seals that maintain tight interfaces under hot, chemically aggressive conditions.
Composite ductwork – BMI and other reinforce polymers mold ultra-lightweight ducting able to meet aerospace outgassing standards.
Pump impellers – High-strength polymers like Torlon injection mold impellers that withstand solvents and fuels within industrial pumps.
I hope this gives you a good idea of how thermoset injection molding expands capabilities beyond conventional thermoplastics! Let me know in the comments if you have any other questions.