Your Professional Liquid Silicone Rubber(LSR) Injection Molding Provider
We can offer One-Stop Solution for your silicone rubber project, from design, prototype, LSR injection molding, and mass production.
Full Manufacturing Plants For Liquid Silicone Rubber(LSR) Injection Molding
Baiwe becomes one of the best manufacturers of silicone rubber products in China. Our Liquid silicone rubber(LSR) injection molding technology can meet your high precision silicone rubber parts.
Our factory has passed BSCI certification and we have cleanroom your medical silicone molding requirements.
Just send us your design or your idea, our professional support team will offer you the best solutions for your project.
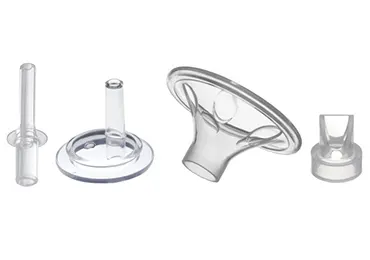
LSR Injection Molding Parts
LSR injection molding parts made by medical-grade silicone gel
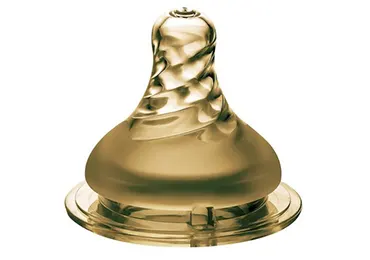
Silicone Pacifier made by LSR Injection Molding
LSR injection molding can make high-quality baby silicone pacifier
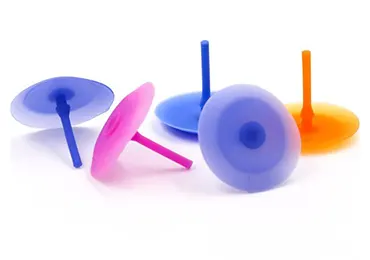
LSR Injection Molding for Medical Silicone Valve
LSR molding can make high precision medical silicone valve
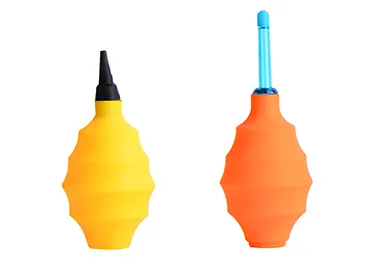
Medical Pressure Ball made by Liquid Silicone Rubber Injection Molding
Liquid silicone molding can produce high standard medical pressure ball
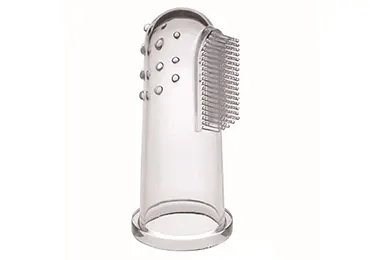
Liquid Silicone Molding for Baby Silicone Toothbrush
Medical silicone molding baby teether custom made by silicone compression molding
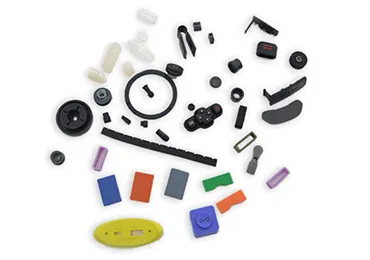
Medical Oxygen Mask made by Liquid Silicone Molding
Liquid silicone rubber injection molding can make high-quality medical breathing mask
Baiwe: We Will Be Your Liquid Silicone Rubber(LSR) Injection Molding Products Manufacturer in China
If you are looking for a manufacturer for your liquid silicone rubber products project, Baiwe would be your trustworthy supplier to make your LSR injection molding orders.
Baiwe is one of the leading manufacturer and supplier of liquid silicone molding, we can custom made any liquid silicone rubber parts as per your demand.
Based on your silicone rubber parts geometry, application requirements, we will offer your our best solutions at a competitive price for your injection molding products.
Contact our support team for your project now!
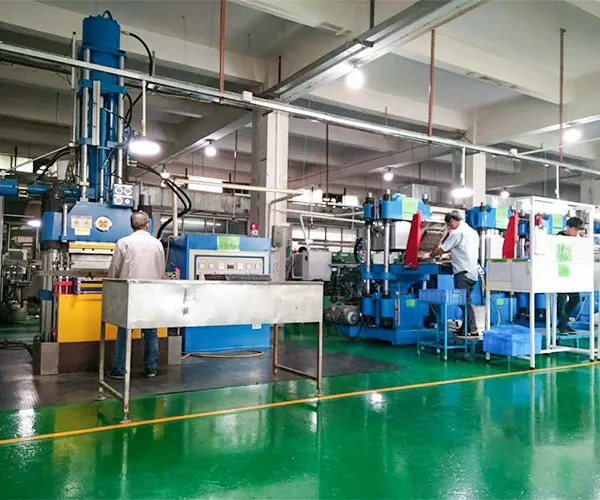
Liquid Silicone Rubber Injection Molding Machine
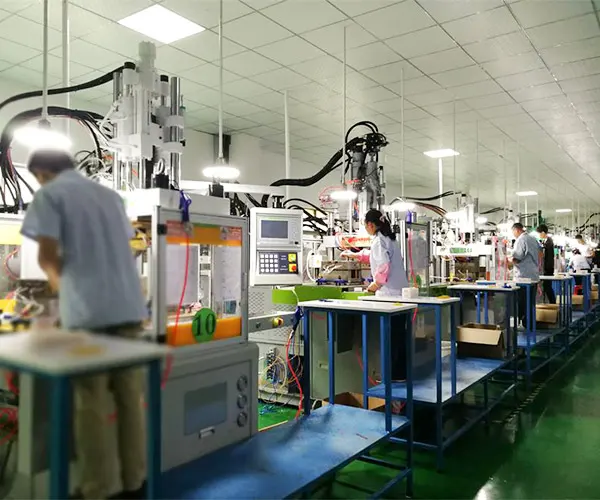
Liquid Silicone Rubber Injection Molding Machine

Die Cutting Machine
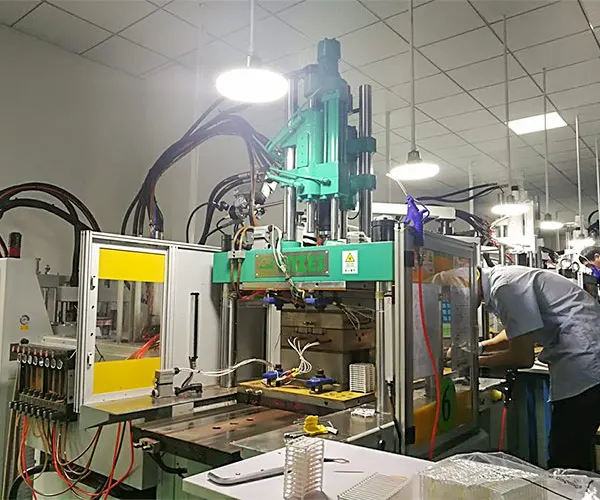
Liquid Silicone Rubber Injection Molding Machine Side

Printing Workshop

Mold Making Machine

Die Cutting Machine

Die Cut Silicone Products Tester

Silicone Keypad Lifetime Tester

Tensile Tester

CCD Tester
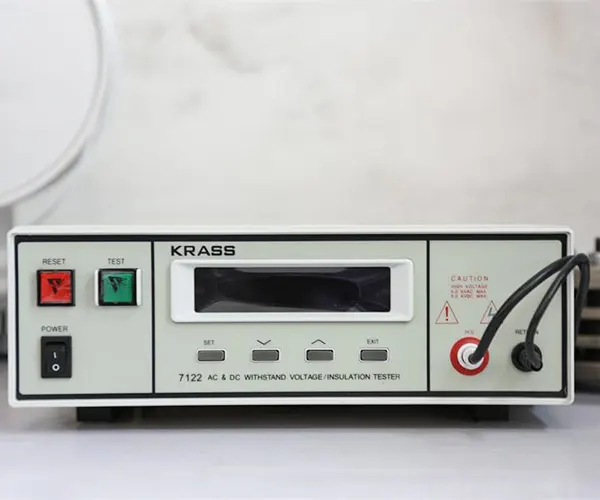
Insulation Resistance Tester
Related Products
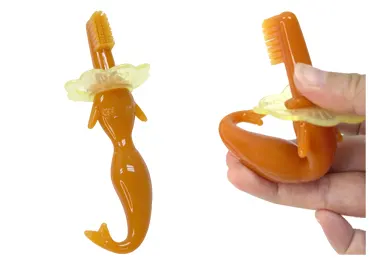
Liquid Silicone Injection Molding-baby Toothbrush
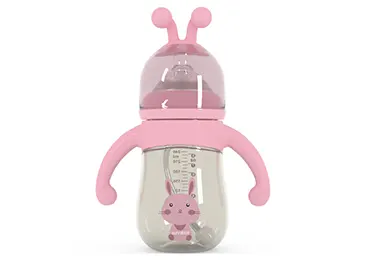
Liquid Silicone Injection Molding-baby Mild Bottle

Liquid Silicone Injection Molding Baby Spoon
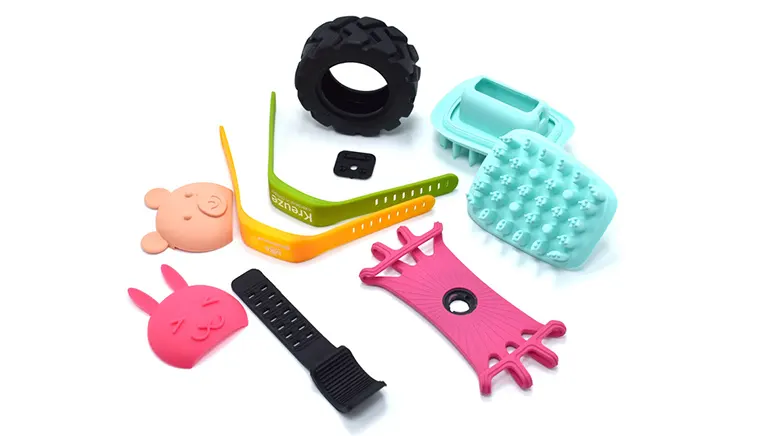
Baiwe: We Not Only Offer Liquid Silicone Rubber(LSR) Injection Molding
We have 3 plants for your different projects. Own-molding plants can offer you fast and economically silicone prototypes. Silicone compression molding plant can meet your regular silicone rubber products and parts. Liquid Silicone Rubber(LSR) Injection can meet your high requirements like medical silicone parts or other high precision industrial silicone rubber parts.
Your One-Stop Supplier For All Kinds Of Silicone Molding Orders
We also can custom made other silicone overmolding products as per your detailed requirements.
Liquid Silicone Rubber (LSR) Injection Molding -The Complete FAQ Guide
- What Is Liquid Silicone Rubber Injection Molding?
- What Is The Method Of Liquid Silicone Rubber Injection Molding?
- What Are The Benefits Of Liquid Silicone Rubber Injection Molding?
- What Are The Downsides Of Liquid Silicone Rubber Injection Molding?
- Which Industries And Applications Are Best Suited For LSR?
- What Are The Types Of Liquid Silicone Rubbers?
- What Are The Characteristics Of Liquid Silicone Rubber?
- What Are The Properties Of Liquid Silicone Rubber?
- How Much Does The Liquid Silicone Rubber Injection Cost?
- What Is The Chemical Composition Of Liquid Silicone Rubber?
- What Material Is Used In LSR?
- Which Industries Have High Demand Of LSR Parts?
- How Does Liquid Silicone Injection Molding Works?
- What Are The Different Type Of Machines Used In Liquid Silicone Injection Molding?
- What Are The Important Considerations In Liquid Injection Molded Design?
- What Are The Material Selection Guidelines For LIM Programs?
- What Are LSR Testing And Inspection Protocols?
- Why Liquid Silicone Rubber Have Become The Ideal Choice For Very Demanding Applications?
- What Are The Quality Standards Of Liquid Silicone Rubber Injections Molding?
- Do Chinese Companies Provide Custom LSR Solutions?
- What Are The Different Types Of Parts That Can Be Achieved Using LSR?
What Is Liquid Silicone Rubber Injection Molding?
LSR injection molding is a process that cools the material delivery system while also heating the mold tool to cure silicon materials into parts.
This method is used when you need to produce flexible, indestructible parts in a large amount.
It also has a shorter cure time when compared to compression molding.
This method allows for the molding of complicated geometrics and over-molding.
What Is The Method Of Liquid Silicone Rubber Injection Molding?
Below is the process involved in the liquid silicone rubber injection molding process:
- Liquid silicone is usually provided in either 5-gallon pails or 55-gallon drums and has two parts. Part A and Part B. Colors come in the form of dispersions and are usually 1-3% in weight of mixed silicones.
- The static mixer will have one Part A silicone and one Part B silicone pumped in it through the dousing unit. Color will be pushed in the static mixer through another hose.
- These combined components will then be pushed into the opening of the injection molding barrel via a shut-off valve.
- A shot of cool mixed silicone will be injected into the mold once the components are inside the barrel as the nozzle seals tightly against the mold.
- Then the nozzle shut-off valve will open to inject a certain amount of cool liquid silicone into a hot clamped mold.
- The nozzle shut-off valve will open and the barrel will reverse from the mold. Meanwhile, the screw will start to build another chosen shot of liquid silicone.
- When the silicone gets vulcanized in the heated mold, the clamp will open allowing the parts to be manually removed or be automatically ejected.
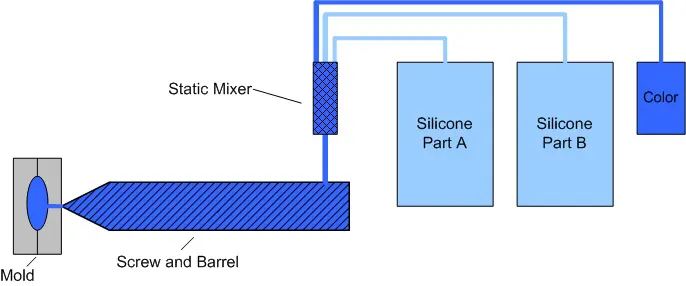
What Are The Up Sides Of Liquid Silicone Rubber Injection Molding?
Liquid silicone rubber injection molding has many benefits and we will take a look at them below.
- It has a fast production time and is highly efficient.
- This method has low labor costs.
- Injection molding allows you to imprint a larger amount of detail on the part as well as manufacture complicated and intricate shapes.
- You can produce thousands of parts before the tooling needs to be maintained.
- Compared to traditional molding methods, injection molding produces very little post-production scrap.
- You can insert any color through masterbatches or compounding.
- Injection molding requires very little post-production work because parts already have a refined look after ejection.
What Are The Downsides Of Liquid Silicone Rubber Injection Molding?
Its benefits are many, right? However, there are also some disadvantages.
- Injection molding has high upfront costs because the method requires a lot of designing, testing, and tooling. There is the general design and prototype stage. Then, a design of the prototype mold tool so as to mass-produce the part.
- You also require a long lead time. To injection mold a part, you will first have to extensively test during both of the above stages.
- Injection molding has many restrictions and rules regarding parts. For example, you have to avoid undercuts and sharp edges as much as possible.
- Because of the complicated tooling, and the need to rid the machine of all previous material before it can run another time, the setup time becomes very lengthy.
Which Industries And Applications Are Best Suited For LSR?
Liquid silicone rubber is an all-rounder material and every day, new applications are discovered and tested. It is the main component in healthcare manufacturing, automotive parts manufacturing, electronics, and consumer products, hardware, and various other markets.
Liquid silicone rubber is used in a wide array of applications that require a high level of transparency, and long-term strength. Some of which are catheters, LED lenses, protective sleeves, optical coupling, and more.

What Are The Types Of Liquid Silicone Rubbers?
There are two liquid silicone rubber types, food-grade, and medical-grade.
- Food Grade: Food grade LSR is suited for manufacturing products that may be purchased by the public. It is the perfect choice if you want to manufacture kitchen products like plastic handles for utensils and cooking tools, baking molds, and more. Its versatile nature and the ability to withstand extreme temperature makes it a perfect choice.
- Medical Grade: It is the preferred choice of people working in life science-related industries, for example, companies that manufacture medical devices. Medical-grade LSR allows manufacturers to produce complicated devices that are technologically advanced. High heat, pressure, and exposure to harsh chemicals are common in the medical environment and medical-grade LSR is capable of withstanding all of it.
What Are The Characteristics Of Liquid Silicone Rubber?
Liquid silicone rubber has become the chosen material for many industries because of its various unique characteristics which are:
- Biocompatibility: LSR easily adjusts with human tissues and bodily fluids as found through vigorous testing sessions. There is also no bacteria growth on LSR and it will not stain or wear away materials compared to other elastomers.
- Strong: LSR can resist extreme temperatures making them the perfect choice for parts that go under the hood of cars and which are close to the engine.
- Resistance To Chemicals: LSR is not affected by water, corrosion, and certain chemical solutions like acids and alkali.
- Resistance To Temperatures: Molded silicone can resist a number of high and low temperatures.
- Mechanical Properties: LSR can be pulled into a long length, can withstand tearing as well as tensile. It is also very flexible and has a hardness range of 5 to 80 Shore A.
- Transparency And Pigmentation: LSR is transparent allowing you to produce molded products that are customized with the color of your choice.
What Are The Properties Of Liquid Silicone Rubber?
Liquid silicone rubber parts are odorless with no taste. Other unique properties of LSR are:
- Resistance to steam and humidity
- Flame retardancy
- Low creep and compression set
- Weatherability
- Vibration absorption
- Corrosion resistance
- UL component recognition and more
How Much Does The Liquid Silicone Rubber Injection Cost?
Tooling costs depend on the size and part detail.
For example, a mold for a seal that is 4″ x 6″ with a .062″ diameter O-ring cross-section may cost around $1500 for a single cavity while $2000 dollars for a double cavity silicone injection mold.
However, a mold that has a complicated gasket with undercuts coupled with a complicated geometry may cost as much as $6000 to $7500 single cavity mold.
What Is The Chemical Composition Of Liquid Silicone Rubber?
Liquid silicone rubber’s attributes are due to its unique chemical composition. It has a two-component system where long polysiloxane chains are strengthened with specially treated silica. Component A has a platinum catalyst and Component B has methyl hydrogen siloxanes as a cross-linker and an alcohol inhibitor.
The liquid” nature of LSR materials sets liquid silicone rubber and high consistency rubber apart from each other.

What Material Is Used In LSR?
LSR is made up of series of silicone dioxide and siloxane bonds that are very strong in properties.
These siloxane bonds are more stable than carbon bonds, and they have superior temperature range performance.
Sand is used in LSR and reacts with methyl chloride that can be formed into several types of silicones.
This leads straight to production of various fluids and polymers, etc.
Which Industries Have High Demand For LSR Parts?
Automotive
LSR is used in the automotive industry because it has toughness, rigidity, high warm steadiness, weakness and tear-resistance.
With different properties, it settles on a great decision for parts utilized in the engine of vehicles.
Numerous OEMs and multi-level care providers prefer to choose LSR to make a wide range of independent parts.
The LSR parts such as silicone O-rings, buttons, accessories, gaskets, and wiring outfit parts are great in demand.
LSR can easily be shaped straightforwardly onto plastic or metal parts which is why it is the best fit for the automobile industry.

Medical and Healthcare
LSR production is also useful in the medical field, and the parts are beneficial for producing health care products.
The clinical grade liquid silicone elastic offers various benefits, like biocompatibility, simple disinfection and simpleness.
The material feels delicate on the skin, which settles on a decision that it is safe as the clinical gadget that contacts the body.
Baiwesilicone offers all kinds of liquid silicone rubber moldings for medical and healthcare products to ensure safety.
Consumer Items
Consumer item industries have a high demand for LSR because silicone rubber gives the crude material enhancement.
It helps to make an expansive range of customer product items.
These products may include some products for showerheads made from plastic to electronic contraptions and jug distributors.
Specialty Applications
Other special uses of LSR in bigger industries are.
- Irrigation and filtration parts
- Pressure check and single direction valves
- Seal rings
- Lighted board buttons
LSR Over-Molding
For the industries that work on the production of gaskets, LSR is very high in demand for such cases because of its properties.
How Does Liquid Silicone Injection Molding Works?
A liquid silicone injection molding can work in different ways in different applications.
A blend of warmth and pressure factor applied to the liquid silicone rubber fixes the material until it sticks properly.
The cycle is repeated, and the shapes are slightly opened, after which it is closed after a few times and rehashes the cycle.
The materials used for the process are acrylics and silicones.
The machine equipment is kept from becoming obstructed with materials.
Then higher infusion strain is allowed from the stacked component that is higher than the pressure factor.
It keeps the channel unblocked and the LIM infusion using a siphon blend with the LSR components.
The fluid blend is then infused into a fixed form where it is warmed at temperatures from 180 to 200 C, or 390 F.
It begins as a liquid and is then warmed inside the shape to start relieving.
When it solidifies, the molding machine discharges the almost completed part.
Numerous producers use PC software like CAD to make the LIM cycle more proficient.
Computer-aided design permits them to run reproductions to decide the most expensive.
What Are The Different Type Of Machines Used In Liquid Silicone Injection Molding?
Supply Drums:
The first type of machine is the supply drums that are used for LSIM.
These drums are directly connected to the pumping systems as the plungers.
They form the LSR supply containers that have two container systems, which also involves a third compartment for pigment.
Metering Units:
There are metering unit machines for liquid silicone injection molding, which have pumps for the two liquid materials.
These pumps are in predetermined ratios, and they help in making sure that a steady ratio for release is maintained.
Mixers:
The mixers are those machines that combine the materials after they are passed through the metering units for liquid forming processes.
It works great for blended material to be pushed into a mold after external pressure is applied.
Injectors:
Injectors help to move the forming material of LSR into the pumping machine so that they can be pressed under force.
The pressure is adjusted to maintain the injection rate and works according to the project specifications.
Nozzles:
Nozzles help to flow the liquid silicone by having an automatic shut-off valve.
This allows controlling the flow of molds through the process.
The mixture of materials and any kind of leakage is avoided through the use of a shut-off valve.
What Are The Important Considerations In Liquid Injection Molded Design?
There are some important considerations in liquid injection molded designs to make a perfect output.
These considerations include.
Part Size
The part sizes should have the following maximum configurations:
- Maximum mold area of 17.6 square inches that is around (113.55 sq cm)
- 5 inches-by-5 inches-by 2 inches (127-mm-into-127-mm-into-50mm)
- The maximum part volume of 4 cubics (65.55 cc)
- 2 inches from any parting line and not deep anymore
Wall Thicknesses
Liquid Silicone Rubber has properties that allow it to be filled in a thin wall section.
The thickness of the wall matters, and it is a requirement that the LSR parts can have a thin wall at 0.010 in. (0.25 mm.)
The recommended rib thickness is 0.5 to 1.0 times the adjacent wall’s thickness.
Mass Reduction and Uniform Wall Thickness
The LSR is applied for a uniform wall thickness because of its superior ability to stick well with wall section deviations.
It reduces the mass of the product, and the design is improved.
Parting Lines
Another consideration to keep is deciding the area of the splitting lines in the tooling system.
To make the cycle simpler, limit the parting or separating lines to deliver cleaner parts and save time.
Undermines
Leaving undermines is also one of the important considerations that are critical for LSR forming.
Most can be eliminated with insignificant exertion by the press service or with mechanical assistance.
This way, each part gets assessed dependent upon the situation for practicality.
Part Removal
LSR moldings have a greater benefit because they don’t need ejector pins for parts removal.
The whole part is held on one portion of the molding when it is opened to the end of the molding cycle.
Under the best situations, the part will transcend the splitting line surface, which makes it simpler to deform.
Draft
LSR parts require a draft for the assembling of the simplicity of the parts.
This includes draft like plastic infusion forming.
Zero drafts can be utilized on shallow parts, while the 1-degree draft is regularly utilized per inch (25.4mm.).
The LSR properties allow adaptability in form development with draft more than it does with thermoplastics.
Venting
The LSR parts require little vents contrasted with infusion formed parts.
Having an entryway or a vent is a must even in the thickest cross-part of any part so that liquid silicone rubber can have a path.
Corner doors are mostly used for most LSR parts that normally make an imprint or flaw.
Tolerances
Resistance is also an important consideration to keep in mind for any LSR mouldings.
Normally, a straight resistance of 0.025 in/in (0.025 mm/mm) is considered for planned parts.
It is must that you start to think for streak remittance.
Baiwesilicone is a manufacturer from China that is offering the best liquid silicone rubber injection moldings keeping all the considerations in mind.
What Are The Material Selection Guidelines For LIM Programs?
Material selection plays an important role in LIM programs.
It is a critical factor that can totally control a successful outcome of a project.
Standard/ universally useful grade Liquid Silicone Rubber doesn’t have a high property of silica.
This makes it fit for applications that require actual essential qualities.
The material selection should be based upon critical upgrades in the item.
This can be based upon the warm soundness, elastic-like characteristics, and protection from ageing.
The expansion of added substances and fillers enable LSR to persevere through higher temperatures, oil, and other liquid conditions.
With the expansion of phenyl units, LSR has more good resistance in low-temperature settings.
Adding phenyl liquid to the material removes the coefficient of grating, and the liquid progressively drains out.
A few categories of LSR give low grating synthetically, which dispenses with the requirement for the liquid to drain to the outer layer.
The material must allow in-shape holding of the LSR to a thermoplastic.
The material must have substance similarity and wear opposition.
It should meet natural and process models as laid out in the project
The left offs can be chosen from various sorts and grades of liquid silicone rubber, from crude to soft ones.

What Are LSR Testing And Inspection Protocols?
The testing standard set for verifying the quality control standards in the manufacturing of Liquid Silicon Rubber is ASTM D412.
This method checks that the component carries out its purpose.
Thermoplastic elastomers and thermoset rubbers are checked for their tensile properties in this procedure.
The method consists of two ways, A and B.
In Method A, a dumbbell-shaped sample is tested with the help of a universal testing machine with clamps.
The other method uses a special clamping mechanism with a ring specimen.
For testing and inspection, the other tests that are conducted are.
- OGP Flash Inspection System
- Video microscope
- Elastomeric physical properties testing
- And also the Elastomeric rheometer
Why Liquid Silicone Rubber Have Become The Ideal Choice For Demanding Applications?
LSR has become the best choice because of its useful base properties.
It has a good ability to remain stable in the long-term use in situations where there are vibrations and exposure to the environment.
It is mold resistant, and any kind of bacteria doesn’t affect its properties as it is hypoallergenic too.
Characteristics of LSR
Durable:
LSR parts can withstand outrageous temperatures, which settles on them an optimal decision for parts in the engine of vehicles.
They are durable parts manufactured by means of fluid silicone elastic infusion.
They are not affected by fire or any liquid material.
Temperature Resistance:
It can withstand a high amount of temperature.
Contrasted with different molded silicone elastomers, can withstand a wide scope of low to high temp limits.
Electrical properties:
LSR has superb electrical properties, which offer an engaging alternative for a large group of electrical applications.
Silicone can act in far higher and lower temperatures as compared to most of the ordinary protecting material.
Straightforwardness and pigmentation:
It has straightforwardness characteristics making it conceivable to create brilliant, exceptionally formed items.
Biocompatibility:
It has a similarity with human tissue and body liquids.
It won’t get stained or erode different materials due to silicone rubber that is impervious to microbes development.
LSR can be designed to be planned to follow tough FDA necessities.
The material can be cleaned by means of steam autoclaving, ethylene oxide (ETO), gamma, e-pillar and various other methods.
Compound obstruction:
Liquid Silicone Rubber has the property to oppose oxidation and water along with other compounds like salt and acids.
Mechanical properties:
Fluid Silicone Rubber has a great extension, high tear and rigidity, magnificent adaptability and a hardness scope of 5 to 80 Shore A.
What Are The Quality Standards Of Liquid Silicone Rubber Injections Molding?
The quality standards set for liquid silicone rubber injections molding are the following.
IATF 16949:2016, ISO 123485:2016, ISO 13485:2016NS-EN, and ISO 9001:2015 are all the quality programs of LSR.
Baiwesilicone company is fulfilling all these quality standards to produce the best Liquid Silicone Rubber in the market.
It is the best manufacturer in China, with overseas customers having deals at wholesales for the best quality LSR.
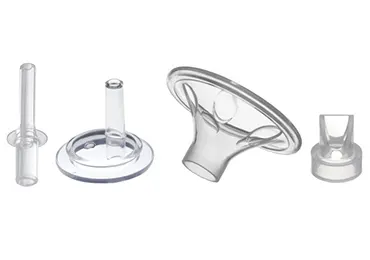
Do Chinese Companies Provide Custom LSR Solutions?
Baiwesilicone is the best manufacturer in China for the production of custom LSR solutions.
Customers can now avail the best custom LSR solutions upon their request from this Chinese manufacturer.
All the items and products are available at a discounted rate, and they are in the best form of quality.
What Are The Different Types Of Parts That Can Be Achieved Using LSR?
There are different production of parts that are achieved by using LSR.
LSR injection molding helps to create complex geometries and automotive parts.
It has the property to join and combine various functional features into a single place.
LSR can be used to achieve the production of medical products that can be used for a lot of purposes.
It can involve drug packaging and wearable equipment in the medical field.
Smart drug pump systems, diagnostic tools and also fluid management parts can be obtained using LSR.
It can also be used to engineer components and to tool for various processes.
LSR leads to the production of high-quality components with high precision in the automobile industry.
There is optimum process automation, and it works best with the lowest cost ownership to deliver different types of parts.
The best parts that can be manufactured are Multi-Component Metal or Plastic to LSR along with Custom Automotive O-Rings.
It has also been found that LSR can help to make Harness Components and Self-Lubricating Components.
Some cases include the production of Anti-Drain Backflow Valves, Spark Plug Boots, Lighted Panel Buttons and Wiring Harness Components.
The extensive use of LSR can lead to Soft-Touch Components, Seals and Gaskets for vehicles, Bellows and Protective Caps.
You also achieve parts for Dampers and Noise Reduction Folds.