Injection molding is one of the most versatile and cost-effective manufacturing processes for producing plastic parts at scale. But with hundreds of plastic materials to choose from, how do you know which one is right for your application?
In this complete guide, as a plastic injection molding manufacturer, I’ll walk you through the most common plastics used in injection molding and help you select the right material for your project.
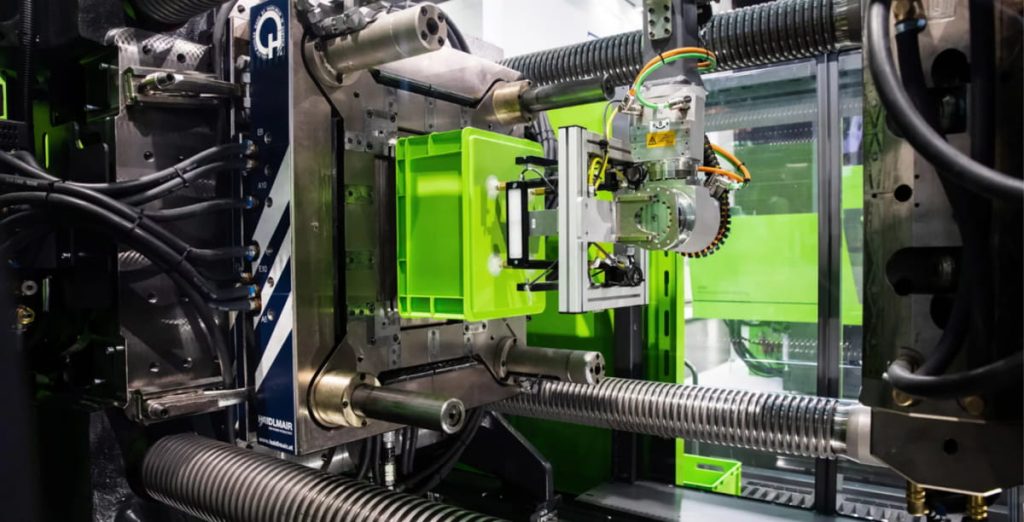
Overview of Injection Molding Plastics
When it comes to injection molding, most plastics fall into three categories:
Amorphous Plastics
Amorphous plastics have a random molecular structure, which allows them to soften gradually as temperature rises. They are excellent at bonding and resisting water. Examples include:
- Acrylonitrile Butadiene Styrene (ABS)
- Polystyrene (PS)
- Polycarbonate (PC)
Semi-Crystalline Plastics
Semi-crystalline plastics contain some crystal structures, so they don’t soften all at once when heated. They share some properties with amorphous plastics but to a lesser degree. Examples include:
- Polypropylene (PP)
- Polyethylene (PE)
- Polyoxymethylene (POM)
Crystalline Plastics
Crystalline plastics have a highly ordered molecular structure, giving them superior strength, chemical resistance, and high melting points. Examples include:
- Polyethylene (PE)
- Polypropylene (PP)
- Polyamide (Nylon)
Now let’s take a closer look at some of the most commonly used injection molding materials.
Most Common Injection Molding Plastics
1. Acrylonitrile Butadiene Styrene (ABS)
ABS is an amorphous plastic that combines strength, rigidity, and toughness at an affordable price point.
It’s widely used for injection molding applications like:
- Electronic housings and components
- LEGO bricks
- Protective headgear and equipment
- Household appliances
- Automotive trim parts
Though not as resistant to sunlight and weathering as other plastics, ABS strikes an excellent balance between cost and performance for both consumer and industrial products.
2. Polypropylene (PP)
Polypropylene is a semi-crystalline plastic known for its moisture resistance, flexibility, and affordability.
Common applications include:
- Food containers and dishwasher-safe items
- Sports equipment
- Automotive components
- Hinges, snaps, and closures
- Packaging and labels
PP is notoriously difficult to paint or bond, but its innate chemical resistance, high melting point, and elasticity make this an ideal resin for products that need to flex without breaking.
3. Polyethylene (PE)
Polyethylene refers to a family of semi-crystalline plastic resins defined by density, ranging from flexible LDPE to rigid HDPE.
Applications depend on the grade but generally include:
- Plastic bags
- Squeeze bottles
- Wire and cable insulation
- Housewares
- Corrugated drain pipes
PE resists moisture and chemicals very well, but much like PP, does not perform well with paints or adhesives. Grades are available for food contact, medical devices, recycling streams, and outdoor applications.
4. Polycarbonate (PC)
Polycarbonate is an amorphous, transparent resin that rivals glass and metal in impact strength.
Typical uses include:
- Eyeglasses and safety lenses
- Riot shields
- Automotive headlamps, lenses
While sensitive to certain chemicals and solvents, PC offers superb optical clarity under extreme temperature shifts, explaining its prevalence in machines and vehicles operated outdoors.
5. Nylon (Polyamide)
Nylon is a unique semi-crystalline plastic available in various density grades. General properties include:
- High strength across wide temperature range
- Resilience to grease, oil, abrasion
- Low coefficient of friction
With its innate slipperiness and mechanical properties, nylon sees frequent use in gears, rollers, bearings, connectors, and even apparel. Flame-retardant grades expand possibilities for electronics and automotive applications.
6. Acetal (POM)
Also sold under the brand names Delrin and Celcon, acetal or POM plastic is a semi-crystalline resin combining three coveted traits:
- Extreme rigidity
- Low friction surface
- Thermal stability
These properties explain POM’s ubiquity in high-wear components like gears, fasteners, latches, and industrial parts needing daily heat and chemical resistance. The material lacks UV stability, limiting outdoor uses.
Other Thermoplastics for Injection Molding
While ABS, PP, PE, PC, nylon, and POM account for ~90% of all injection molding jobs, myriad other plastics bring unique capabilities:
- Acrylic (PMMA): Optical clarity for lighting, point-of-purchase displays
- Polyurethane (TPU): Resilient elasticity for sporting goods, wearables
- Polysulfone (PSU): Retains strength and clarity up to 300°F+
- Polyetherimide (PEI): Withstands sterilization, radiation without distortion
- Liquid Crystal Polymer (LCP): Dimensional stability across broad temperature shifts
Nearly all plastics can be injection molded with the right equipment and process tuning. Specialty engineering resins push the limits of performance but usually cost more.
How to Select an Injection Molding Plastic
Choosing a resin comes down to your product requirements, production goals, and budget. Key considerations include:
- Mechanical properties: Impact strength, rigidity, max load capacity
- Thermal traits: Upper temperature limit, cold impact resistance
- Aesthetics: Optical clarity, texture, post-mold surface quality
- Chemical exposure: Will material contact solvents, oils, or corrosive agents?
- Part costs: Material price per lb + additives + processing
- Sustainability: Recycled content, recyclability, carbon footprint
Thoroughly examine your application to identify must-have traits, then cross-reference resins to find matches. Don’t assume only basic polymers like PP or PE apply. Today’s filled compounds and exotic blends offer tailored solutions.
Reach out to experienced injection molders like The Rodon Group early in design with your “wish list” and challenges. Their expertise steers you to cost-effective options.
Common Applications of Injection Molded Plastics
Thanks to its versatility, injection molding produces infinite products across every industry:
Automotive
- Taillight covers, connectors, fuel system parts
- Steering wheels, knobs, interior trim
- Under-hood components able to withstand extreme heat
Consumer Electronics
- Smartphone and laptop cases / bezels
- Power adapters, controllers, remote housings
- Liquid crystal displays (LCDs)
Medical & Laboratory
- Multi-well plates, tubing, cables for devices
- Pipette tips, vials, culture flasks
- Diagnostic equipment casings resistant to chemicals
Food & Beverage
- Clear packaging clamshells, containers
- Caps, spray nozzles for condiments, cleaners
- Appliance housings, refrigerator parts
Injection molding brings the performance, consistency, and economies of scale needed for mass production across industries. Just ensure you first select a plastic resin matching your exacting needs.
Key Takeaways
- Hundreds of plastic resins exist but amorphous, semi-crystalline and crystalline polymers account for most injection molding jobs.
- Leading resins include ABS, PP, PE, PC, nylon/polyamide and POM/acetal plastics.
- Select your material based on mechanical, thermal, chemical and aesthetic requirements.
- Injection molding enables cost-effective, scalable plastic part production for virtually any industry.
Carefully assessing applications and vetting material options prevents problems, from embodied carbon emissions to product failures. If questions remain about your path forward, reach out to an expert for guidance. The right solutions bring peace of mind today and better outcomes for tomorrow.