Injection molding is one of the most popular manufacturing processes for mass production of plastic parts. However, despite being a mature technology, it continues to pose production challenges that manifest as defects in the final products.
As a professional plastic injection molding manufacturer, I have dealt with countless issues that crop up in our production lines from time to time. In this detailed guide, I’ll discuss the most common injection molding problems our industry faces and how to avoid them through proper design and process control methodologies.
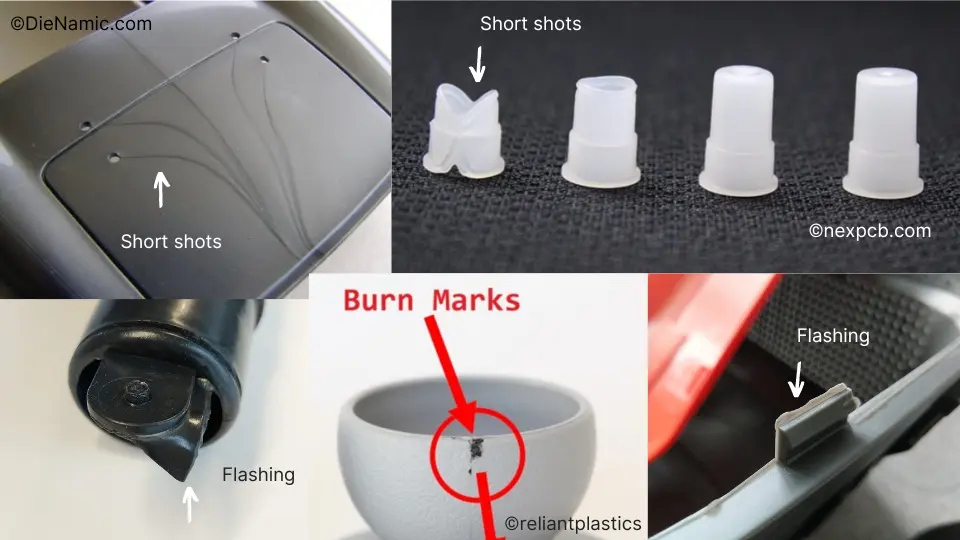
Why Injection Molding Defects Happen
Before we get into the specifics, it’s important to understand what causes these issues in the first place. Generally, injection molding problems arise due to two key reasons:
1. Improper Part or Mold Design
A wrongly designed part or mold is often the root cause of production issues. Common design mistakes like uneven wall thickness, improper gate placement, insufficient draft angles and more can hamper flow and cooling inside the mold cavity.
The end result is defects on the plastic part’s surface or vital dimensions being out of spec. In extreme cases, bad designs also lower mold longevity and lead to downtime for repairs or new tool fabrication.
2. Incorrect Process Parameters
Even if the mold and product design is optimal, the injection molding process needs to be finely tuned through machine settings. Factors like injection pressure, speed, barrel temperatures and cooling time directly impact the molded part’s quality.
Operators need proper training to correctly identify and set these parameters. A tiny oversight can manifest as visual or dimensional defects. Moreover, process variations due to environmental factors also play a role.
Now that we know what generally causes injection molding defects, let’s discuss the most common ones plaguing the industry and how to avoid them.
6 Common Problems with Injection Molding of Plastic Parts
Warpage
Warpage refers to unintended distortions or bends on a plastic part as it ejects out of the mold. It mainly occurs due to non-uniform shrinkage as the hot plastic part starts cooling inside the mold cavity.
Factors contributing to warpage defects include:
- Uneven wall thickness in the product design leading to uneven cooling
- Low clamping force allowing the part to detach from the mold surface as it cools
- Insufficient cooling time before the part gets ejected
- Improper gate and runner system design impeding uniform flow inside the cavity
A warpage defect not only impacts appearance but can also alter critical dimensions; especially in precision components.
To avoid warpage, manufacturers must:
- Simulate filling and cooling inside the mold cavity using Moldflow analysis before finalizing the product design
- Ensure uniform wall thickness through optimization
- Increase cycle time to allow gradual cooling before ejection
- Maintain adequate clamping force through process control
Sink Marks
These appear as small indents or depressions on a plastic part’s surface, especially around thicker wall sections. As the name suggests, sink marks “sink in” due to non-uniform solidification as thicker areas cool slower.
Typical causes of sink mark defects include:
- Low injection pressure providing inadequate packing
- Insufficient cooling time before ejecting the part
- Very high melt or mold temperatures increasing solidification time
- Bad design with uneven wall distribution or improper rib placement
Besides marring surface aesthetics, sink marks also indicate possible structural weaknesses in that area.
Some ways to prevent sink marks are:
- Optimize product wall thickness and rib distribution to ensure even cooling
- Increase cycle time and cooling period before ejection
- Add sufficient injection pressure for packing
- Lower barrel temperatures to quicken solidification
- Use a material grade that crystallizes faster
Flash
Flash refers to thin layer of plastic protruding from the parting line or ejector pin areas – basically anywhere the two mold halves meet. It occurs when the mold doesn’t close properly, allowing hot plastic to seep into tiny gaps.
A flashing defect results due to:
- Insufficient mold clamping force
- Worn out or damaged mold halves with uneven surfaces
- Excessive injection pressure or speed breaching the parting line
- Poor venting leading to trapped air pressure breaching gates
While mostly a cosmetic issue, flash can impact assembled part functionality, cause moving interferences or hurt operator handling.
Effective flash prevention involves:
- Inspecting and maintaining mold halves to ensure proper alignment and contact
- Adding sufficient vents for trapped air escape
- Lowering injection pressure and velocity
- Increasing clamp force tonnage as per required cavity pressure calculations
Short Shots
Short shot refers to incomplete filling of the mold cavity due to early solidification. This leaves certain sections underfilled or significantly thin. Apart from surface defects, short shots also severely impact strength and function.
Typical short shot causes include:
- Low barrel or mold temperatures leading to early freezing
- Inadequate injection pressure and velocity
- Very high mold complexity with long flow lengths or thin walls
- Blocked gates or vents preventing cavity access
Solutions to avoid short shots:
- Optimizing gate locations and sizing for balanced fill
- Increasing injection fill velocity and pressure
- Using mold temperature controllers for consistency
- Making sure vents are clear through mold maintenance
Weld Lines
Weld lines occur when two flow fronts of plastic meet from different directions, creating a visible mark on the part surface. They indicate incomplete knitting or bonding between polymer layers.
By acting as stress concentrators, weld lines significantly lower strength.
Weld lines can occur due to:
- Excessive cooling before convergent flows meet
- Non-uniform melt temperatures
- Low injection pressure or velocity
- Bad design with hole placements or inserts
Some ways to prevent weld line defects are:
- Increasing mold and melt temperatures
- Optimizing gate locations to control flow sequence
- Adding vents near expected weld line areas
- Increasing injection speed and pressure
Burn Marks
These appear as black or brown burnt spots on the plastic part near the gate, especially in corners. Burning occurs when trapped air or excess resin get overheated due to excessive shear.
Typical reasons behind burning include:
- High injection speed forcing air pockets
- Small gates preventing trapped air outlets
- Insufficient vents to release trapped gases
- Excessive screw RPM introducing air via plastication
Burn prevention requires:
- Reduced injection speeds with controlled acceleration at the end
- Larger width gates and optimally places vents
- Monitoring screw RPM and backpressure
- Lower barrel temperatures
In Summary
By understanding common injection molding defects, causes and remedies, manufacturers can produce better quality components, lower reject rates and maximize productivity. The solutions outlined above serve as a practical guide to get started but eventually process control through scientific molding principles is key for consistent defect prevention across production batches.