Injection molding produces stronger parts than 3D printing. Injection molded components have higher strength due to the way the molding process works and how layers bond together. As a professional plastic injection molding manufacturer, I will explore why injection molding makes stronger parts in this article.
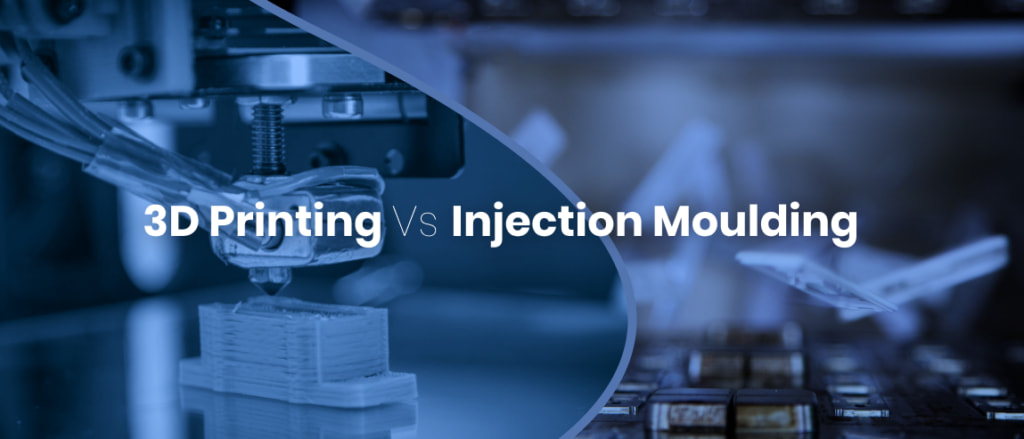
How injection molding creates stronger plastic parts
When it comes to strength of plastic parts, injection molding has some inherent advantages over 3d printing. The injection molding process produces complete interlayer bonding, resulting in stronger cohesion between the molecules. This makes injection molded components more rigid and durable.
On the other hand, 3d printed components are made by depositing material layer-by-layer. Even with a good 3D printer and optimal settings, each new layer still has small gaps between the previous layer’s molecules. So even if the extruded plastic molecules bond well on each new layer, the layers themselves don’t bond perfectly to each other.
This small gap between layers is usually 10-50 microns. While tiny, these small gaps still allow for delamination between layers when enough shear force is applied to a 3D printed part. In contrast, injection molded parts have continuous bonds between molecules throughout the entire part with no gaps or potential delamination points.
Key factors that make injection molding stronger
Several key characteristics of the injection molding process contribute to stronger plastic parts:
- Single poured layer – Molten plastic fills every corner of an injection mold tool’s cavity in a single pouring phase. The plastic solidifies as one continuous piece with strong intermolecular bonds.
- Alignment – Polymer chain molecules align under the pressure and friction within the injection mold tool’s cavity. Chain alignment contributes to strength.
- Pressure – High pressure (around 15,000 psi) packs together polymer chains tightly and eliminates gaps or air pockets. This maximizes bonding between molecules.
- Tool finishing – The mold tool’s polished surface imparts a smooth, glossy finish. This eliminates stress points along a part’s surface.
In essence, an injection mold tool compacts together plastic molecules in the tightest possible alignment under high heat and pressure. Parts demolded have a dense molecular structure with continuous bonds throughout, free of gaps or weak points.
How 3D printing’s layering process limits strength
Fused deposition modeling (FDM) printers deposit plastic filament layer-by-layer to build up parts. Each new layer bonds reasonably well to the last. But gaps between layers keep parts from reaching maximum strength. Other 3D printing processes also build parts in layers, creating similar bonding issues between deposited material.
Several characteristics inherent to 3D printing limit part strength:
- Layer gaps – Typical 3D prints have small gaps between layers, usually around 50 microns (0.002 inches). These tiny gaps concentrate shear forces and allow layers to separate under stress.
- Layer misalignment – It’s essentially impossible to perfectly align long polymer molecules between printed layers. Chain misalignments between layers create weak points.
- Anisotropic strength – Due to differences in bonding between and across print layers, FDM parts have directional weaknesses. For example, pulling force across layers causes easier breakage.
- Voids – Tiny air gaps between filament lines are common on each deposited layer, further reducing strength.
- Porosity – Some 3D printing methods use powders. Particles don’t completely fill space between layers, creating small pores. These pores act as stress concentrators.
In general, weaker bonding between print layers creates built-in planes for shearing, cracking or delaminating when under significant load. Parts tend to fail easily across layer lines.
Strength test comparisons affirm injection molding’s advantages
published experimental results directly comparing strength between injection molded and 3D printed test samples. Their data clearly shows injection molded components have markedly higher tensile, flexural and impact strengths.
For example, their ABS samples showed the following strength differences:
- Tensile strength – Injection molded ABS: 45 MPa vs. 3D printed ABS: 28 MPa
- Flexural strength – Injection molded ABS: 75 MPa vs. 3D printed ABS: 60 MPa
- Impact strength – Injection molded ABS: 25 KJ/m2 vs. 3D printed ABS: 3 KJ/m2
The researchers attribute the strength differences to voids within layers and variable necking between rasters for 3D printed parts. This confirms the inherent strength limits related to weak bonding between print layers.
Interestingly, annealing improved mechanical properties for 3D printed components by approximately 20%. This heat process partially “heals” layers together. But annealed parts still did not reach the strength of injection molded components.
Factors that help improve 3D printed part strength
While injection molding produces stronger plastic parts, 3D printing excels at prototypes, custom parts, and short runs. Prints make excellent fit and functional test articles.
For end-use parts, designers should orient prints to load forces along rather across print layers. Part strength also improves with these measures:
- Minimize part height to shorten layer stacking
- Use 100% infill instead of a lattice for max density
- Choose optimal print orientation to reinforce against operating stresses
- Anneal parts to better bond layers together
- Use secondary plating/coating to add rigidity and toughness
When to choose injection molding or 3D printing
For critical components that experience high static or dynamic loads in service, injection molding provides superior mechanical properties. It makes sense for long production runs where tooling costs can amortize over thousands of molded parts.
But for iterative designs that change frequently or lower quantities, 3D printing allows faster design adjustments. Small batches of functional prototypes or custom end-use parts are more affordable to print versus injection molding with costly steel tooling.
Consider both additive and molding processes during your manufacturing process planning to leverage their respective advantages. Often, combining them creates the most efficient path to final production.
Why is injection molding stronger than 3D printing?
To recap, injection molding imparts considerably greater strength to plastic parts compared to 3D printing. Layer bonding mechanics fundamentally limits 3D printed components from reaching the same rigidly and durability as injection molded parts.
The high pressure injection process neatly packs together long polymer molecules in the tightest alignment possible within a mold’s cavity. Parts demolded have a dense, continuous matrix of plastic free of weak points or gaps.
In contrast, 3D printing’s additive nature creates small but significant layer interface gaps between deposited Roads. Differences in layer-to-layer molecule alignments also contribute to anisotropic weaknesses.
So for ultra-strong production plastic components that experience high mechanical stresses, injection molding makes the most sense based on performance requirements. Ideally combine it with 3D printed prototypes earlier in product development to leverage both technologies’ advantages.