SILICONE COMPRESSION MOLDING
Advanced Equipment Silicone Compression Molding Factory
As one of the best silicone compression molding manufacturers, we have a full set of audits, BSCI, SGS, FDA, and LFGB. We have a mold-making workshop , silicone compression molding workshop,injection molding workshop, printing/coating workshop, also have advanced equipment for your silicone rubber products.
If you are looking for a supplier for your silicone compression molding project or orders, pls send us your specific details, and we will offer you our best price.
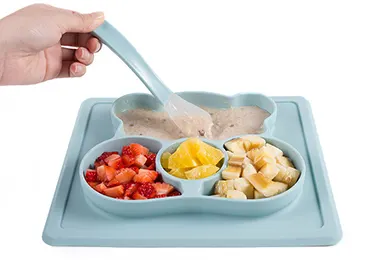
Silicone Compression Molding Baby Food Tray
BPA free baby food tray made by silicone compression molding
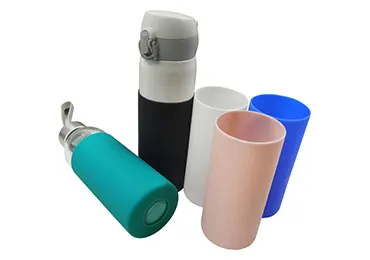
Silicone Compression Molding Bottle Sleeves
Customized bottle sleeves made by silicone compression molding
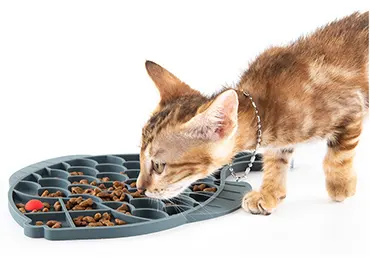
Silicone Compression Molding Pet Food Tray
Fish shape silicone pet food tray
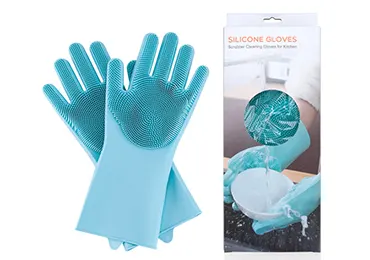
Silicone Compression Molding Gloves
Silicone gloves with brush made with silicone compression mold
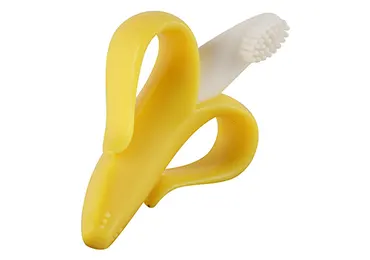
Silicone Compression Molding Teether
Medical silicone molding baby teether custom made by silicone compression molding
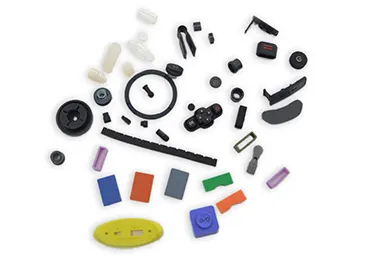
Silicone Compression Molding Molded Parts
Different kinds of silicone rubber compression molding molded parts
Baiwe: One-Stop Solution Provider For Your Silicone Compression Molding Project
Please tell us if you are looking for a silicone compression molding supplier for your customized silicone rubber parts, we would be your best choice.
Baiwe is a silicone compression molding manufacturer and was found in 2005 in the south of China, with 15 years of growth, we have passed the BSCI audit and our product was approved by SGS, FDA, and LFGB. Your every order will be guaranteed with good quality.
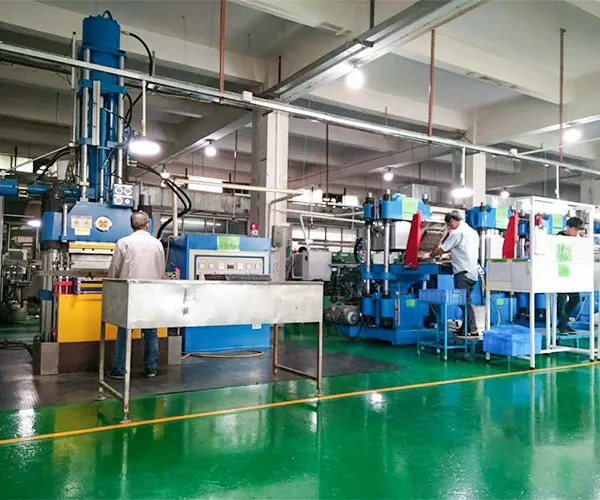
Liquid Silicone Rubber Injection Molding Machine
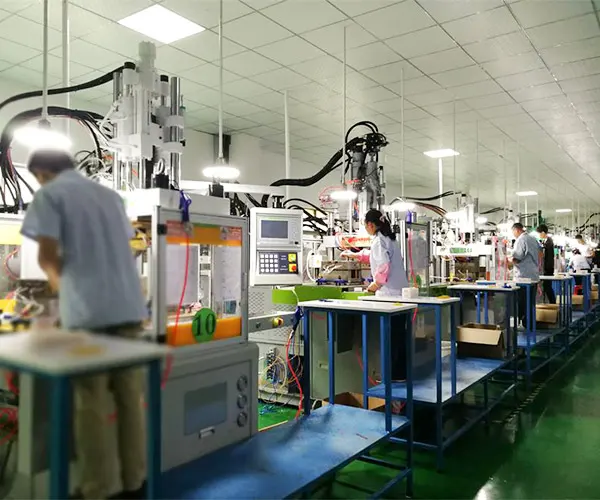
Liquid Silicone Rubber Injection Molding Machine

Die Cutting Machine
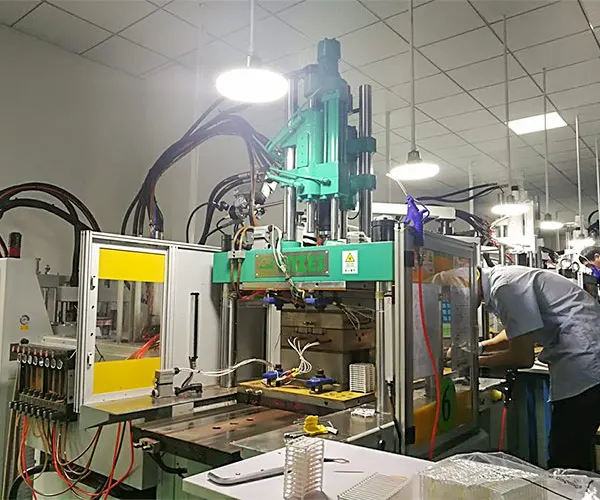
Liquid Silicone Rubber Injection Molding Machine Side

Printing Workshop

Mold Making Machine

Die Cutting Machine

Die Cut Silicone Products Tester

Silicone Keypad Lifetime Tester

Tensile Tester

CCD Tester
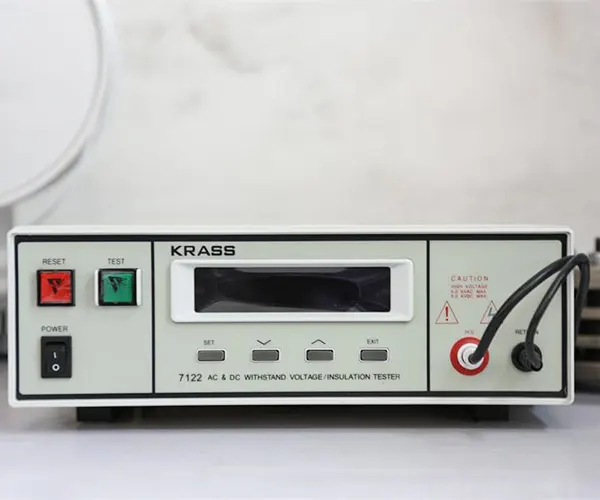
Insulation Resistance Tester
Related Products

Silicone Compression Molding Pet Food Tray

Silicone Compression Molding Water Bottle

Silicone Compression Molding Kitchenware Set
Baiwe Silicone Rubber Compression Molding Accept Small Quantity For Your Order.
Baiwe has its own mold-making plant, we can accept low MOQ if your silicone rubber order is not big. Our professional design team can offer free 3D design, you can send us your physical samples, drawing, even your ideas. You won’t be regretful to choose us as your silicone rubber compression molding manufacturer.
We Can Custom Made For Your All Kinds Of Silicone Rubber Parts
Silicone Compression Molding- Everything You Need To Know
- What Is Silicone Compression Molding?
- What Is The Method Of Silicone Compression Molding?
- What Is The Typical Temperature For Silicone Compression Molding?
- What Are The Benefits Of Silicone Compression Molding?
- What Are The Downsides Of Silicone Compression Molding?
- What Are The Properties Of Silicone Compression Molding?
- What Are Silicone Compression Mold Types?
- Silicone Compression Molding Is Suitable For?
- How Much Does Silicone Compression Molding Cost?
- Silicone Compression Molding VS Silicone Injection Molding
- What Is The Process Of Silicone Compression Molding?
- What Are The Other Material Options Available For Compression Molding?
- What Are The Equipment Used In Silicone Compression Molding Process?
- What Are The Manufacturing And Quality Standards For Silicone Compression Molding?
- What Are The Component Of Rubber Compression Molding?
- What Engineering Process Is Involved In The Silicon Compression Molds?
- What Is A Two Basic Plates Mold Type Of Compression Molding?
- What Is A Basic Plate With Middle Plate Type Of Compression Molding?
- What Is A Two Basic Plate With Mold Core Type Of Compression Molding?
- What Is A Basic Mold Plates With Sliders Type Of Compression Molding?
- What Is The Best Source To Buy Buy Silicone Compression Molding Service?
What Is Silicone Compression Molding?
Silicone compression molding is a tried and trusted method of manufacturing silicone parts. The process is the same as making waffles in a waffle maker.
A certain amount of uncured silicone rubber is placed in a mold cavity which is closed and heated. When the parts are cured, they are removed from the mold.
Compression molds can produce the widest range of part sizes ranging from 0.024 inches to 30 inches in diameter.
What Is The Method Of Silicone Compression Molding?
Silicone compression molding involves several steps:
- An uncured silicone rubber slug is formed to the required shape and size based on the finished part. The uncured silicone slug is termed preform because it is ready to be formed, or molded. Each mold will have a different shape and size perform that suits best.
When the perfect preform has been determined, It is important to have resilience in both its size and shape to make sure the part forms correctly. Excessive material is wasteful and can cause the flash to become too thick and too little material causes voids in the parts.
- The preform is placed inside the cavity of a heated mold and the mold is closed. Heating and pressure are applied in the compression molding press. A logic controller monitors and controls critical aspects such as temperature, pressure, and time to ensure molding takes place within a prescribed resilience window.
- The mold is opened and the cured silicone rubber is removed along with its flash.
- The part is moved through the manufacturing process to go through the post-molding process which may include deflashing, post-curing, automated inspection, and packaging.
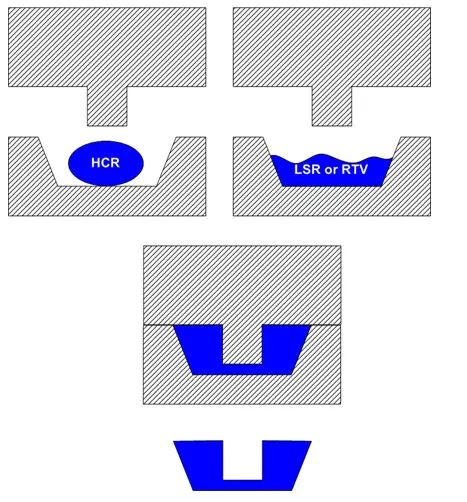
What Is The Typical Temperature For Silicone Compression Molding?
An average compression molding process is performed at a mold temperature of 350℉ with a mold pressure of 100 psi (180℃ and 700 kPa) which has a curing time of 3 minutes.
After the material is done curing, the mold is opened and the silicone part is pushed out. Compression molding is a cheaper process compared to others and is capable of high volume production.
What Are The Benefits Of Silicone Compression Molding?
Below are the many advantages of silicone compression molding:
- The loss of raw material is minimal and will not cause too much loss, usually 2% to 5% of the product quality.
- The internal stress of the end product is low as well as a small warping deformation while the mechanical properties are stable.
- The life of the mold cavity is small with a low maintenance cost.
- Molding equipment also costs less and the mold structure is simpler. You can produce multiple cavities at a low price and compared to injection molding it has a lower manufacturing cost.
- It is suitable for large flat products. The size of the products that can be molded through this method is determined by the mold clamping force of the mold pressing machine and the size of the mold plate.
- If you require parts in batches, compression molding is suitable at a relatively low price.
- Molds that have a high number of cavities can be placed on a certain plate to improve productivity.
What Are The Downsides Of Silicone Compression Molding?
Below are some of the disadvantages of silicone compression molding:
- The overall molding cycle is long with low efficiency. The time needed to start and repeat the whole process is between 1- 6 minutes.
- Currently, it is not recommended if you want to mold complex products that have depressions, side slopes, or small holes.
- Should burrs occur, they will have to be trimmed manually which will reduce productivity as well as increase labor costs and material wastes.
- In compression molding, the manufacturing is complicated combined with a large investment. The compression machine is also limited and is suited for mass production of small and medium composite products.
What Are The Properties Of Silicone Compression Molding?
Compression molding has environmental versatility and high chemical resistance. You can produce buttons, gaskets, respirator masks, spatulas, and syringe stoppers through the compression molding process.
Compression molding is perfect for any industry that needs versatile compound requirements to meet the performance criteria of parts, parts that have difficult to mold geometry, and prototypes that require material of choice. Compression molding also works if you need dual material molding.
What Are Silicone Compression Mold Types?
From a mold structure perspective, compression molding has 4 types:
- Two Basic Plates Mold: It is the most common and simplest rubber compression mold. This mold is suitable for rubber parts such as silicone o ring or flat nitrile rubber gasket.
- Basic Plates With Middle Part: This mold is suitable for rubber products that have small undercuts like rubber grommet seals.
- Two Basic Plates With Mold Core: This mold is suitable for products that have deep undercuts and cylinder-shaped rubber parts such as silicone bottle sleeves.
- Basic Mold Plate With Sliders: This method can be used with complicated silicone rubber parts that have deep under or hollow cylinder shapes.
Silicone Compression Molding Is Suitable For?
Compression molding is suitable when you want to insert, fabric, and encase molding for prototypes with simpler handling and faster process development.
If you need to prototype silicone micro molded parts, compression molding is perfect due to controlled handling, shorter tooling and process development time, and overall lower costs.
How Much Does Silicone Compression Molding Cost?
A general prototype used to produce simple parts such as a grommet for compression molding costs $750 to $1500.
If it is a multi-cavity compression mold, its benefits are the number of parts it produces per hour. A typical 6 cavity compression mold can easily manufacture 40 to 50 parts per hour. If you want to spend a little more on the mold to create more cavities, it will increase the parts per hour and decrease the unit cost to below $5.
Silicone Compression Molding VS Silicone Injection Molding
Silicone compression molding and silicone injection molding have five differences that set them apart. Size of product, production time, quantity, quality, and shape of final products. We will examine them below:
Size Of Product: Compression molding is suitable for creating large silicone products while injection molding is suitable for smaller silicone parts that have high tolerances. Compression molding also allows the production of products that vary in wall thickness from 1.3 mm to an inch.
Production Time: Compression molding has a longer production time compared to injection molding. Furthermore, if there is excess flesh around the parts, it will have to be trimmed manually in compression molding. This will slow down the production cycle and make the process more labor intensive. Injection molding, on the other hand, is completely automated making it more efficient.
Quantity: An automated process combined with a short cycle time gives place to high-quantity production. For this, injection molding is more suitable. Compression molding is perfect if you want a low and medium series of large products.
Quality: Injection molding is used if you want a part that has strength.
Shape Of Final Production: Products in compression molding are simple. The silicone is cut into a shape that resembles the final product ( which is usually simple). While in injection molding you can manufacture more complicated rubber parts like cones. These products can have varying degrees of wall thicknesses and can combine different shapes.
What Is The Process Of Silicone Compression Molding?
The process of silicone compression molding is very simple and easy to understand for those who have even the littlest of knowledge.
All you need is mold cavity, alignment bushings, mold plates, and pins that are useful to complete the process.
You need a separate place for uncured rubber preform where you can inject it easily.
This process is used in high-pressure situations, which involves the use of a vulcanized rubber that is shaped into a useful rubber part.
These rubber parts are helpful for removing friction and reducing noise in moving parts of machines.
Compression molding is a very cost-effective technique as compared to injection molding because of its use with NBR, SBR, EPDM etc.
The rubbers formed by compression molding can support high performing machines that are running for big businesses.
Compression molding causes the creation of high-quality rubber parts which are durable and stress-free.
These parts are homogenous, and they can be used in a variety of applications and sold worldwide too.
Different types of equipment are used in the compression molding process to transfer molding and to make it very cost-effective.
What Are The Other Material Options Available For Compression Molding?
The most common type of material option used for compression molding is Thermoset composites.
The process of compression molding involves the use of thermosetting plastics.
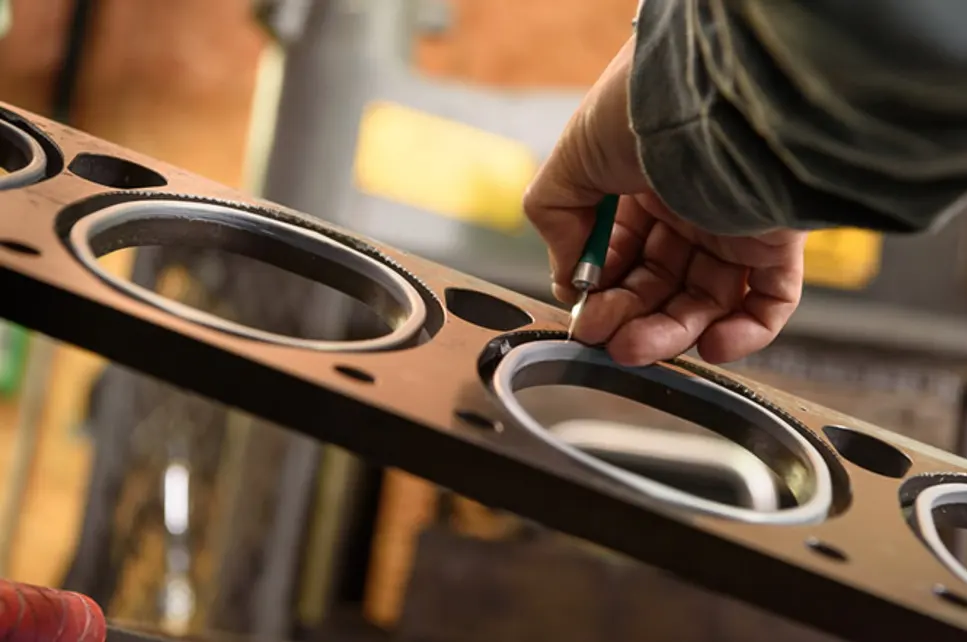
Polyurethane, urea-formaldehyde, Bakelite, polyester, melamine, epoxy, as well as alkyd resins, are used in compression molding.
A sheet moulding compound is also useful in the process of compression molding.
Compression molding is a flexible method for fabricating things like thermoplastic polymer by using glass mat thermoplastics.
The materials that are generally manufactured in the process of compression molding are Torlon and Vespel.
Polyester Fiberglass resin systems and polyphenylene sulfide also play an important role.
A thermoset plastic material is also used as viscous material that is in flowing granular form.
When compression molding takes place at a mold temperature, the intermediate material being used is called moulding compound.
What Are The Equipment Used In Silicone Compression Molding Process?
The silicone compression molding process is tricky and tough that is carried out by experts with the right equipment.
This process must involve equipment like mold cavity, mold plates, pins and alignment bushings.
The mold plates and mold cavity are placed to hold everything together and are stronger.
Alignment bushings play an important role to keep the product aligned in a stable form while pins give it a firm grip.
You must have a place where you can inject the uncured form of rubber, which will be very cost-effective for you.
What Are The Manufacturing And Quality Standards For Silicone Compression Molding?
The manufacturing and quality standards for silicone compressing molding in China is of the following standards.
- RMA Class A – Tolerances for O-ring
- ISO3601-1 Tolerance for O-ring
- Rubber Manufacturers Association, RMA-A2
- ISO 3601-3 Grade N and Grade S tolerances
Baewisilicone is the best manufacturer in China that sits well on these standards for quality in the manufacturing of these moldings.
You can place your orders to get the package in bulk for your business from this industry.
What Are The Component Of Rubber Compression Molding?
There are different components of rubber compression molding, and they include a lot of processing for getting a final form.
Heat is introduced to a raw rubber which is then bonded with sulfur to carbon-hydrogen chains to form a link.
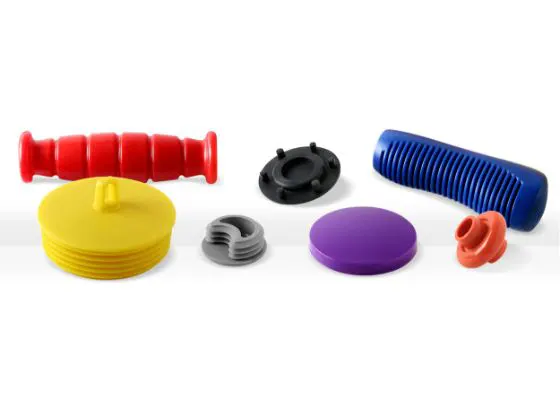
It becomes a shape randomly, and the components lock together pretty well.
Rubber compression takes place after getting the heat when chemicals work in place, and then cooling is applied to the form.
This process creates compounds, and the resulting parts have the ability to stand against high temperatures.
This is the place when vulcanized rubber is then introduced and used for rubber compression molding.
What Engineering Process Is Involved In The Silicone Compression Molds?
Engineering is very critical in silicon compression molds, and it’s very important to handle the vulcanized rubber to achieve rubber parts.
To start the process, the engineers have to take care of these factors.
- The flexibility of rubber and its quality material that is being applied.
- The pressure will be applied during the compression molding process.
- Weight of the overall part when it is being formed.
- Thermal decoupling of the process.
- Vibration dampening during the process of silicone compression molds.
- Mechanical condition and properties of the machines during the running process.
Contingent upon the kind of item being made from this cycle, it should precisely line up with these determinations.
The calculation and materials are changed by engineers before the pressure forming measure even starts.
Whenever the situation allows, it should be properly given the time and attention to carry the process safely.
There are CAD programming tools that can support these calculations.
Modern 3D displaying permits you to compute the volume of rubber required significantly.
What Is A Two Basic Plates Mold Type Of Compression Molding?
The two basic plates silicone compression mold is a common rubber compression mold that is simple in design.
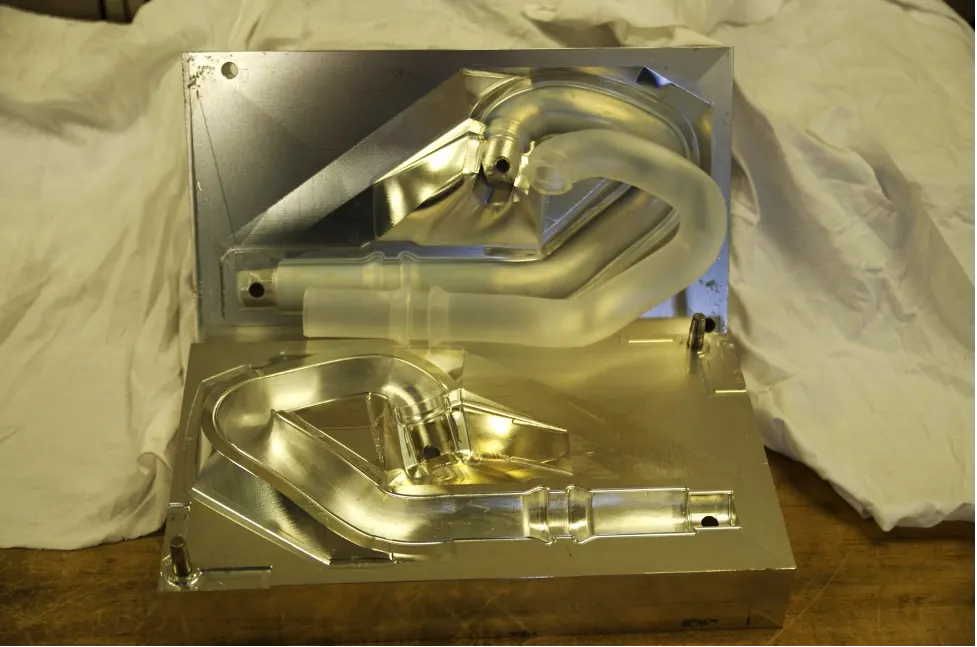
In this, there are two tool plates having product cavities in them, and they can be used compression molding processes like cold and hot.
These are best suitable in situations where the company needs to develop simple and useful rubber parts.
Silicone O ring and flat Nitrile Rubber Gasket are two good examples.
What Is A Basic Plate With Middle Plate Type Of Compression Molding?
A basic plate having a middle plate type of compression molding is the Cavity plate.
This type of plate is for filling the gaps, like creating a cavity through that gap and filling it with plastic material.
It helps to form plastic components.
The middle plate helps to direct the cavity place and then leaves an empty portion for the plastic material to be filled in.
It is suitable for a situation where rubber products with small undercut grommet seals are required.
What Is A Two Basic Plate With Mold Core Type Of Compression Molding?
For the products that have deep undercut and are cylindrical in shape, compression mold with mold cores are used.
The rubber parts like silicone bottle sleeve and grommet are used where rubber is demolded from its mold cores.
Parting lines or separating lines are placed on both sides of the rubber in the type of basic plate with a mold core.
What Is A Basic Mold Plates With Sliders Type Of Compression Molding?
The rubbers parts that are very complex in their shapes having hollow cylinders and shapes require sliders type of compression molding.
This type of molding design can take a longer cycle time for molding with sliders.
It is because the sliders need to demould or take out the rubber seals.
You can expert a short mechanical lifespan with such type of compression molds.
The lines for parting in this type of compression mold are clearly visible with the duration of time.
What Is The Best Source To Buy Silicone Compression Molding Service?
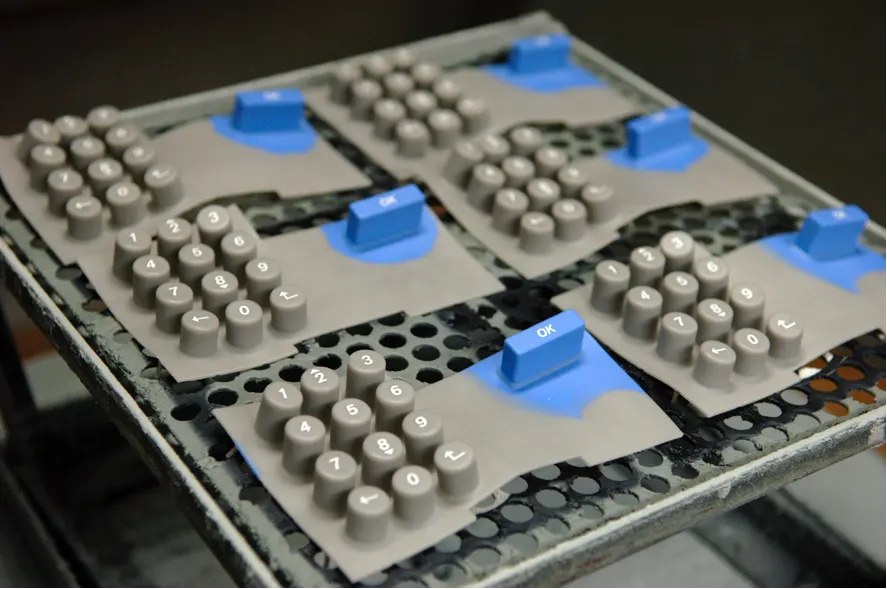
It is the best and leading source in China, which can be relied upon because it follows all the quality standards of silicone compression moldings.
They are also offering their services overseas to international clients as well.
Are Chinese Silicone Compression Molding Service Different From European Services?
The Chinese silicone compression molding services are a bit different from European services with greater benefit.
Chinese manufacturers are leading the business with 75% in the ratio for silicone compression molding business in the global market.
It is because the molding services offered by China are very cheap in price provided with the quality and satisfaction in one place.
The best manufacturers in China, like Baiwesilicone, keep a deep check on the market trends and provide the best services for moulding.
This is the reason that Chinese silicone compression molding services are different from European services.